Estimated reading time 12 minutes, 3 seconds.
When Jack Frost comes to town, the Snowball dance starts at Toronto Pearson International Airport.
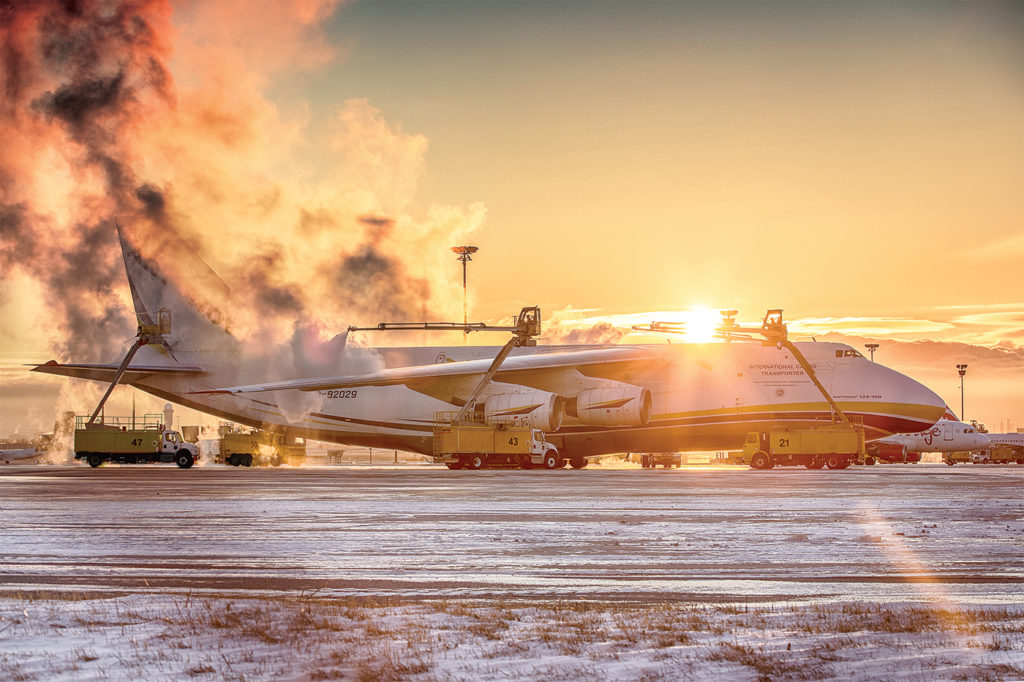
It’s a highly choreographed performance, with the Snowballs starring alongside the Iceman, Frosties, and Polar Bears–and even Whiskey plays a supporting role.
All of these unusual call signs represent assets belonging to the Central Deicing Facility (CDF) at Canada’s busiest airport.
The cutting edge centre opened in 1998 on a 65-acre parcel of land at the south end of Pearson. At the time, it was lauded as the largest and most advanced centralized deicing facility in the world. Many airports were still deicing aircraft right at the departure gates, a practice that is widespread even today.
But Pearson recognized the advantages of a centralized facility that would be more efficient at processing aircraft, while enabling stricter environmental controls that would drastically reduce the amount of glycol making its way into nearby Etobicoke Creek.
Today, the CDF may be 20 years old, but it still sets the standard.
“I would say we’re probably the industry leader here,” said Ken Eastman, director of deicing operations at the facility. “That’s due to some of the technology we’ve implemented, such as our bay management system, telemetry in the trucks, [and] our automated deicing communications system that lets us communicate from the electronic flight strip to the trucks.”
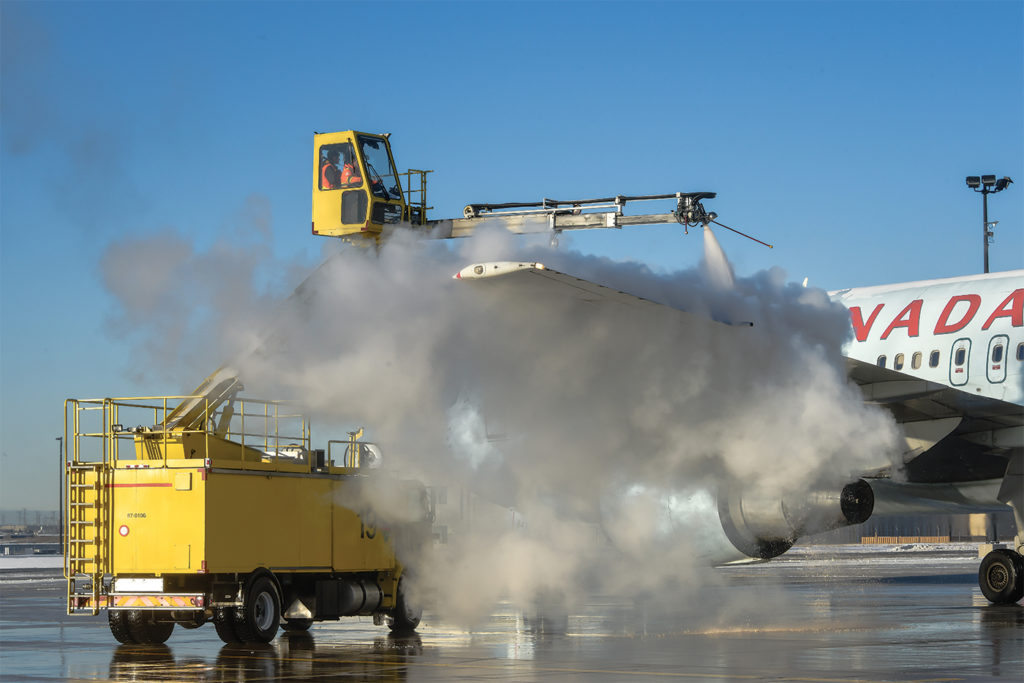
At peak capacity under frost conditions, the CDF’s projections show it could handle 60 aircraft in an hour. While Eastman said they haven’t yet experienced that level of demand, he added that a typical narrow-body deicing under those weather conditions should take less than 90 seconds.
The CDF’s six deicing bays can accommodate 12 narrow-bodies, six wide-bodies or any combination thereof–and the same number of aircraft can be staged behind them, ready to go.
“Last year, in December [2016], we put 51 aircraft through here in an hour under light snow conditions.”
Eastman, who has worked at the CDF since it opened, explained that two types of glycol-based fluids are dispensed at Pearson. In frost conditions, an orange liquid heated to at least 65C and known as Type 1 deicing fluid, is sprayed over an aircraft’s critical flight surfaces, most importantly its wings and tail.
In active precipitation conditions–moderate snow, for example–the CDF carries out a second application of green anti-icing fluid. This Type 4 mix is a more viscous fluid that soaks up precipitation and is effective for a prescribed time, allowing an aircraft to taxi and take off safely. As soon as an aircraft picks up speed and rotates off the runway the fluid shears off, leaving a clean surface, explained Eastman.

Deicing season can stretch from September to May, and while every year is different, on average the CDF goes through about 7.5 million litres of Type 1 fluid and two million litres of Type 4 fluid per season.
“The one question we always get asked is, ‘Do you have enough fluid?’ This facility actually ran out of fluid during an ice storm in April 2003 or 2004. That’s when we started blending and making our own fluid here to have twice the supply,” said Eastman.
Now, glycol is delivered on consignment in concentrate form. Depending on the weather forecast, the CDF has the ability to increase or decrease the concentration of glycol in the fluid. On the bitterly cold day that Skies visited, the CDF was applying a 44 per cent Type 1 blend.
Eastman noted that the ability to blend various concentrations helps mitigate deicing costs for operators. A 44 per cent blend costs about 80 cents a litre. It will take approximately 300 litres to treat a Boeing 747 in frost conditions, while a narrow-body will require about 100 litres.
So what happens to all of that used glycol?
With each of the six deicing pads sloped from north to south, spent deicing fluid trickles into special catch basins and then into diversion vaults where it is tested onsite by wastewater technicians. After testing, the fluid is diverted to one of the CDF’s massive underground storage tanks, with a combined capacity of 15 million litres.
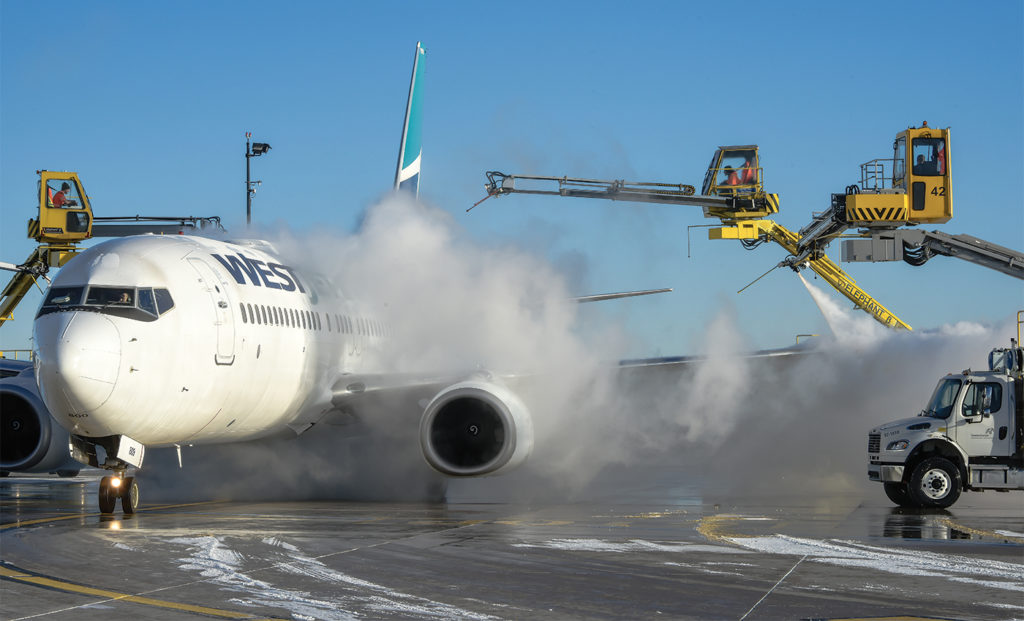
“Because of our location, we can release fluids to the City of Toronto or the Region of Peel,” explained Eastman. “Anything that is three per cent or higher in glycol is captured and kept. Anything lower is released to the sanitary systems based on our BOD [biochemical oxygen demand] limits as allowed.”
Stored fluid is sent to a glycol processing facility, where it is brought back to a 50 per cent glycol concentration and then sold in the after-market, in products such as automobile windshield washer fluid.
To further safeguard the environment, the CDF’s entire ramp was built on top of a bonded membrane that prevents used glycol from seeping into the ground.
Equipment and Technology
The CDF is a progressive facility that has kept up with the times.
For example, of the facility’s 46 total deicing trucks (also known as “Snowballs”), about half of them have the technology to blend glycol mixtures on board.
“As we continue to re-life the equipment, we will get to the point where we can blend the fluid of the day on all trucks,” said Eastman. “What we do now is we make batches of fluids, based on the weather forecast, and it goes out in the pipeline and the trucks fill up.”
Another fact that makes the Toronto facility unique in North America is that it is the only one with underwing deicing trucks (call sign “Whiskey”).
“What that does is it gives us the ability to spray the underwing or undercarriage of the aircraft and not have to shut the aircraft down, or put someone on the ground around the aircraft.”
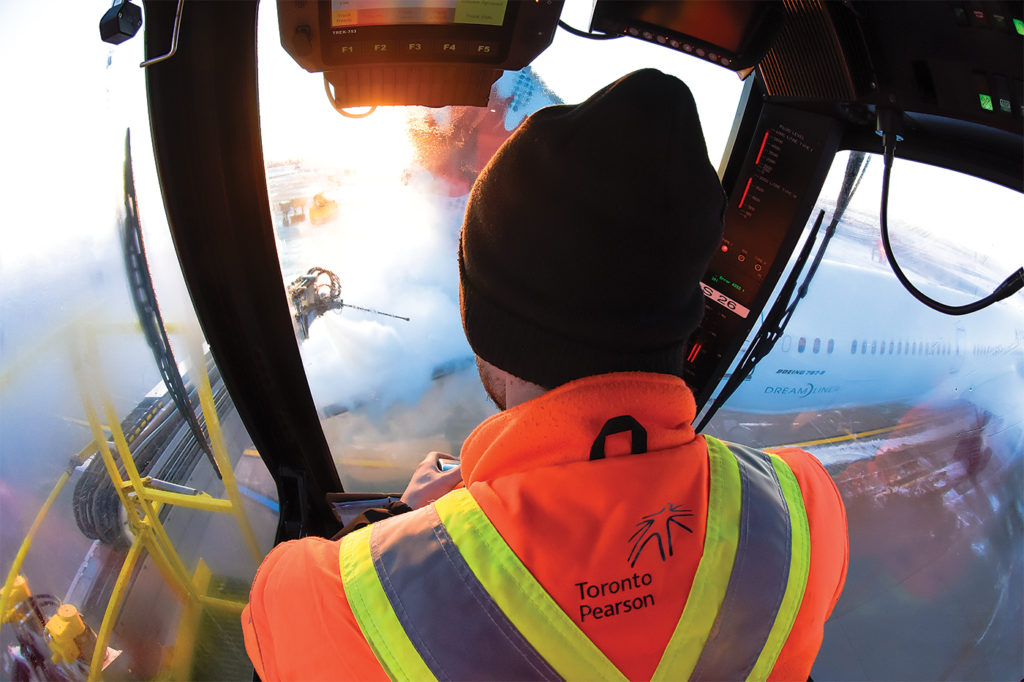
Also hard at work out on the ramp are support trucks called “Frosties” and technical inspectors (codename “Quebec”) who are responsible for supervising spray patterns and performing quality checks. Glycol recovery vehicles (“GRVs”) also roam the ramp, vacuuming up excess glycol and collecting the fluid for processing.
The ground floor of the Ice House is home to the “Polar Bears”–also known as supervisors. Upstairs in the control room, a half dozen deicing movement coordinators (including a zone deicing coordinator (“Zulu”), Iceman North and South, pad controller and a bay manager) stare intently at a series of screens, occasionally glancing up through the wraparound picture window to watch an aircraft taxi into position for deicing.
Sometimes, they will use closed-circuit TV cameras to zoom in on an aircraft’s wings or tail to inspect for contamination. Other monitors keep them informed of the current fluid levels in each truck.
When aircraft arrive for deicing, pad control will take over from air traffic control (ATC) and direct them to the South Iceman (pads 1, 2, 3) or North Iceman (pads 4, 5, 6).
The zone deicing coordinator oversees the resources being applied and then the electronic flight strip goes back to the Iceman–who speaks with the flight crew directly during the deicing process. The Iceman then passes the flight strip back to pad control, who will exit the aircraft and transfer it back to ATC.
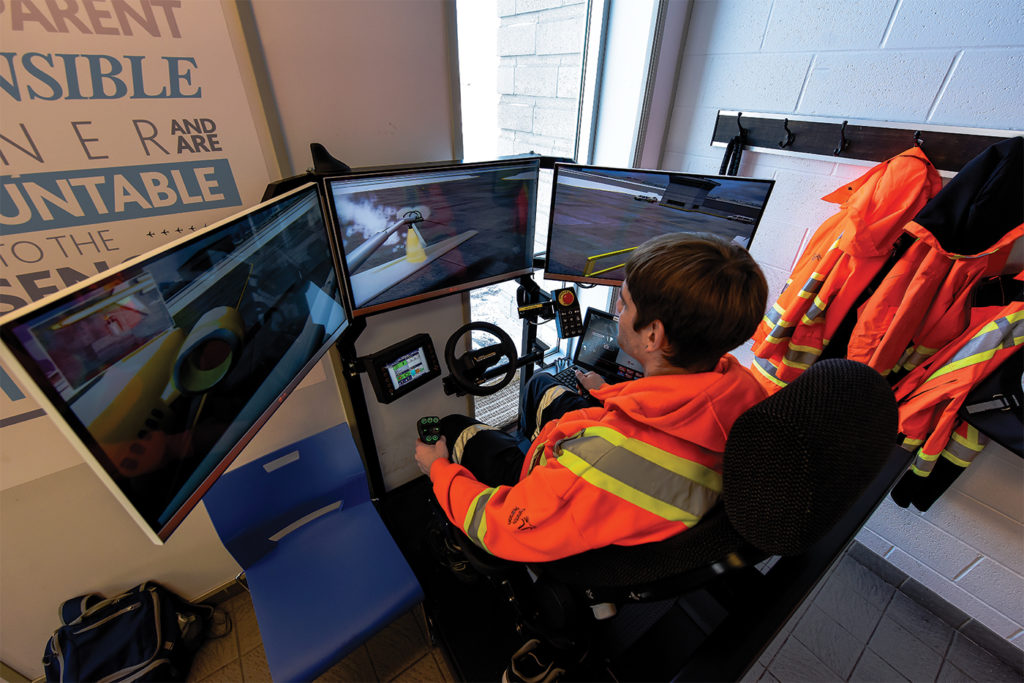
Once activated, flight strip information is forwarded to computers in the Snowballs. Deicing specialists confirm information and check off the work as it is performed.
In total, Toronto Pearson’s Central Deicing Facility is home to 180 employees. Seventy-eight are seasonal workers, while the remainder comprise the year-round staff.
“We have a core group, and we use them to maintain this facility,” explained Eastman. “Underground, those tanks all need to be cleaned. The entire core group is confined-space trained, so they take care of looking after the fresh glycol farm and the underground tanks. The team will go down in the summer and clean them all out.”
The CDF is staffed around the clock for 365 days a year, although a skeleton crew holds down the fort in the summer. Sometimes, they are needed to direct traffic on the pad surface during lightning advisories or other extreme weather events.
The summer of 2018 will see lots of activity on the CDF grounds.
“Right now, we have a project in to put another five-million-litre storage tank underground,” said Eastman. “They can only work in that area over the summertime. Construction will run from April to November; then they will close it up and do the mechanical work underground. When it’s done, our capacity will be 20 million litres underground.”
The new underground tank resulted from a CDF optimization study carried out in the summer of 2017. Eastman said they also examined the projected demand for deicing services over the next five years, realizing that the peaks and valleys are filling in.
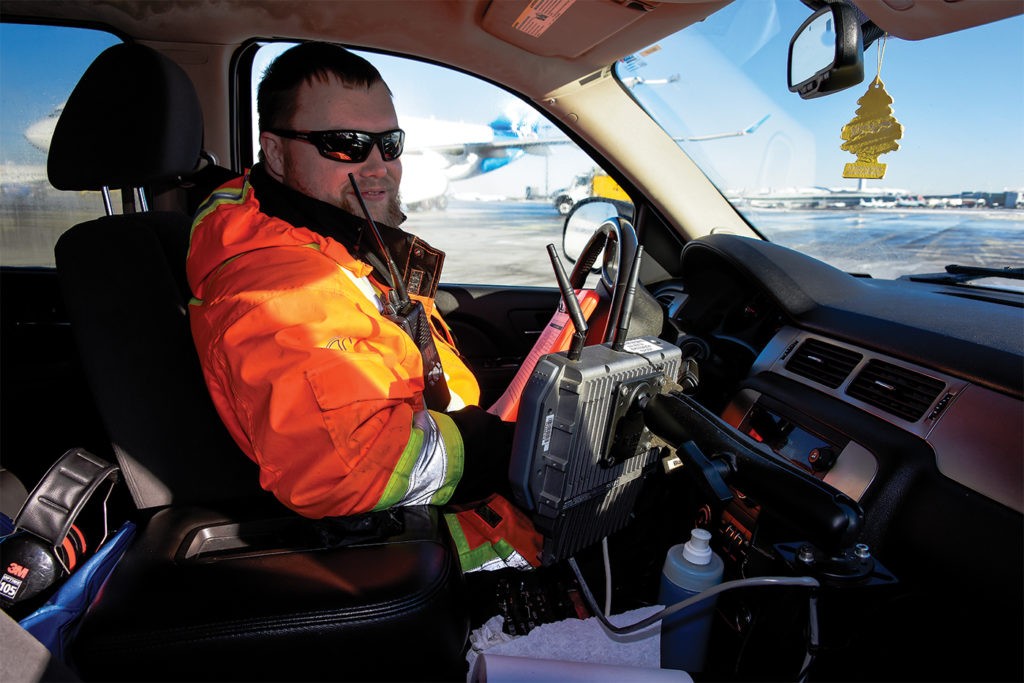
“What do we need to do for air carriers to meet schedule resiliency? Yes, we can meet the demand under certain conditions, but when we’re in a Type 1 and Type 4 procedure, we may not be able to keep up with demand,” he pointed out. “We looked at widening a pad and maybe adding two additional pads, so that no matter what conditions we’re in, we could keep up
with demand.
“We’re looking to see how we can optimize this existing real estate, increasing our resources, as well as looking at the benefits of expanding our capacity here.”
While the location of those potential new pads is still to be determined, there is no doubt that the Pearson facility is moving to meet future airport growth.
According to the Greater Toronto Airports Authority, Toronto Pearson International logged 384,481 aircraft movements in 2016; and although final 2017 data had yet to be published at the time of writing, all indications were trending upward.
Finally, Eastman revealed that architects are in the early stages of planning a new five-storey Ice House that will be more than twice the size of the existing building, to be constructed over the CDF’s current parking lot.
A Seamless Production
Passengers might be in a hurry to take off, but for those who take the time to observe the deicing process, it’s an impressive sight that could almost be set to music.
Aircraft are guided into the deicing bay by large electronic signboards, with green chevrons advising them to move forward until they are in the correct position.
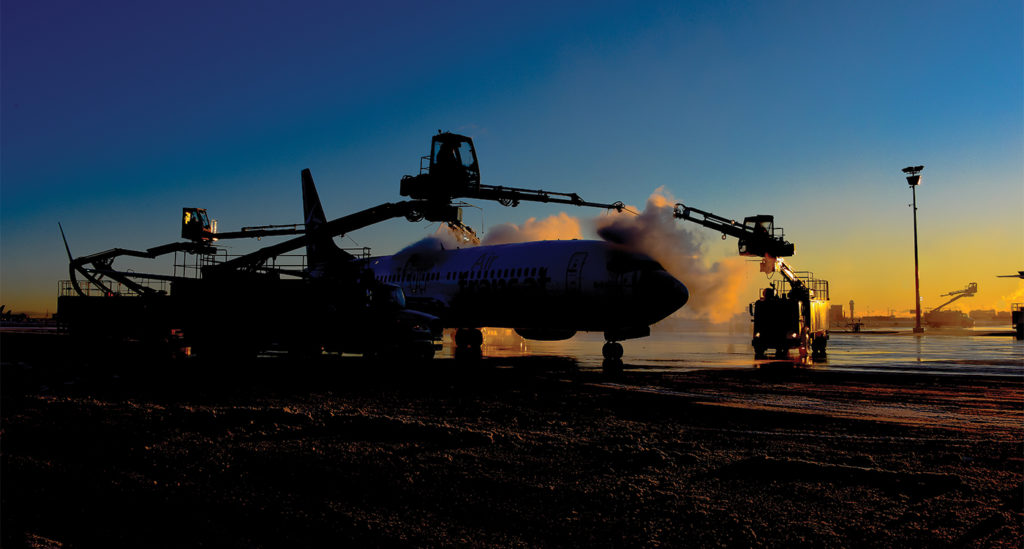
Once the aircraft is stationary, two to six Snowballs will approach. Each $1.25-million truck can be driven from the deicing specialist’s aerial cab, allowing for one-person operation. Their movements are precisely choreographed to match set patterns determined by aircraft type, with technical inspectors looking on to ensure procedures are followed to the letter.
When the truck is in position, a telescoping application arm extends and a joystick in the truck’s aerial cab controls the glycol dispersal in sweeping movements. As the hot Type 1 fluid meets the cold wintry air, steam rises into the sky.
Within seconds, the trucks exit the deicing area and the aircraft is inspected and then cleared to depart the bay.
Even live propellers can be sprayed, with the glycol applied to the leading edge, although aircraft do need to be shut down for treatment if they have contamination on the prop surface.
As for business aircraft, Eastman said those that are hangared don’t need deicing, while the rest will visit the CDF. Under certain conditions, a prescribed number of slots is available for Pearson’s business aviation community.
Future Focus
As the CDF plans to expand its physical surroundings, it is also hiring to meet the growing demand for its services.
Thirty-four new deicing specialists were brought on at the end of 2017. The organization promotes from within, and five of the six staff members working the control centre on the day Skies visited used to spray planes.
“It’s up and down, this job,” said Eastman. “[The] stress level depends on weather. You need the ability to get your game going instantly if the weather changes.”
After two decades of being at the top of its game, Toronto Pearson’s CDF remains a leader in North America. It’s not unusual to see representatives from various airports visiting the centre to observe and learn from its operation.
Visitors to the Ice House are always welcome–in fact, they’re given a front row seat to view one of the finest choreographed performances in winter airport operations.